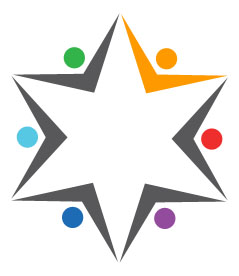 |
(½-day)
When beginning any new initiative - such as Lean or Six Sigma - it is natural that some
people react with skepticism.
The goal of this workshop is to build unit-wide interest in
the adoption of Lean or Six Sigma through the clarification of key concepts, benefits, a hands-on experience of a Lean Six Sigma process, and, if appropriate, the provision of reassurance regarding
feared outcomes (e.g. job loss, etc.).
This workshop can be tailored to its audience, whether front-line employees, middle management, or an executive team.
Workshop Approach
Participants will participate in a simulation activity that
requires top-quality work to be performed quickly for the benefit of a
client. As the simulation unfolds,
participants will recognize many everyday working
conditions that act as barriers to success.
Upon solving the simulation task, participants will realize that Lean
systems and processes are the key to success. They will experience first-hand how individuals
can work under less pressure, with less risk, and more enjoyment while producing higher-quality results and improved client satisfaction. They will be excited that they solved the simulation themselves, and will be interested in learning more about how to improve
“broken” processes and how to incorporate more “common sense” into their work in
a systematic way.
Throughout the simulation and after, Lean language and
concepts will be introduced and demystified.
If appropriate, unit-specific goals
and current plans for incorporating Lean will be presented. The pros and cons of maintaining the status
quo will be compared to those of incorporating Lean through participant
discussion.
The workshop will end with a Q & A session. Participants will have the opportunity to ask
the facilitator about Lean practices and concepts. More importantly, they will be able to ask
unit leaders for reassurance regarding fears related to the incorporation of
Lean.
Agenda
- Involve learners in an engaging mini-Lean experience
- Connect the experience to basic Lean concepts
- Identify positive outcomes of incorporating Lean practices; examples specific to your industry will be used where available
- Reassure unit members regarding potential negative outcomes of incorporating Lean practices (e.g. downsizing)
- Share current business unit goals and plan for incorporating Lean practices (e.g. upcoming training, projects, etc.)
- Q & A
|
|
|
(2 days)
A business process map is a simple diagram that contains a great deal of information about how things get done in the organization.
Organizations use business process maps to:
- Show auditors that safe, sound, repeatable processes for important activities exist
- Understand how things actually get done in their organization
- Understand the differences between how things should get done and how they actually get done
- Identify weak spots in processes that cause errors, delays, and extra costs
- Form a foundation for continuous improvement and risk-reduction efforts
- Quickly and effectively help new employees to understand their roles
The most useful business process maps incorporate input from the employees who work in the process. These reflect a true picture of how work is performed, and why the process works well or sometimes fails.
This workshop is designed to enable participants to efficiently and effectively map business processes based on employee input.
By the end of this workshop, you will be able to:
- Explain the elements of a business process map
- Choose the most appropriate level of a process to map
- Choose the scope of a process to be mapped
- Record a SIPOC high-level version of a process
- Use a variety of symbols to record process events including tasks, decisions, delays, transmission of information or paperwork, database storage, inspections, parallel activities, and more
- Incorporate employee experiences and discussion into the mapping of a process
- Ask appropriate questions of leaders and those who perform the work to determine the actual steps in a business process
- Collect and arrange information about a process in an Excel spreadsheet
- Draw a flow diagram
- Draw a commercial process map
- Explain the principles of well-designed processes
- Identify and record process benchmark metrics
The workshop will be highly interactive, and will include valuable hands-on activities.
|
|
|
(2 days)
WorkOut is a rapid, team-based problem-solving process
developed by General Electric, and used by many world-class companies. It is known as the “fast-track to process
improvement”. WorkOuts involve people who work in a business process; they may work in one department or across the organization. Their "insider knowledge" of the process is used to understand and improve it. Through participating, their skills,
confidence, and engagement grow, while business problems are resolved.
WorkOuts are used to:
- Streamline and simplify business processes
- Fix problems that frustrate employees and clients
- Reduce bureaucracy, costs, defects, time-wasters, and other
non-value-added activity
- Shift an organization's focus from complacency to improvement
- Capitalize on employee knowledge using an efficient,
practical process
- Empower employees to identify, select, and implement
solutions
- Replace blame and finger-pointing with shared ownership and
commitment
During a WorkOut, selected employees meet for 1-2 days to
systematically review a problem and develop solutions. Low-investment/high-return solutions are
recommended for implementation, and are presented to management for approval prior
to the end of the meeting. Typically,
management chooses to implement 90% of the recommended solutions based on
their high quality and feasibility.
Group members implement solutions in the workplace over the next 30 – 90
days with the manager’s support.
WorkOut solutions have very high success rates due to the
participatory nature of the process.
Management finds that solutions are effective, results can be achieved
quickly, and a have a high degree of support and sustainability within the
organization.
This workshop will provide participants with the concepts,
processes, skills, and practice needed to facilitate WorkOuts within the organization.
Workshop Outline
1. Introduction to WorkOut
- Purpose and background
- Phases of WorkOut
- What is a Business Process?
2. Participation in a “Mini WorkOut”
3. Key Skills & Tools: Running the WorkOut Meeting
- Welcome, Introductions, and Climate Setting
- Setting Group Guidelines
- Process Mapping
- Identifying Process Issues
- Categorizing Barriers (Affinity Diagram)
- Prioritizing Barriers (Dotmocracy)
- Brainstorming Tips
- Managing the Payoff Matrix
- Action Planning
- Facilitating the Management Decision Making Process
4. Key Skills & Tools: Preparation for WorkOuts
- Identifying Whether WorkOut is the Right Tool
- “Selling” WorkOut
- Issue Identification
- Contracting With Management
- Preparing Management for its Role
- Who to Invite?
5. Key Skills & Tools: Follow-Up to Ensure Implementation of Plans
- Roles of Facilitator, Manager, and Participants
- Follow-Up Support Techniques
- Reporting
5. Practice and Integration: Participant-Facilitated Mini
WorkOut
- Facilitate mini-WorkOut based on a case study
- Discussion: Preparation for using WorkOut in the workplace
|
|
|
(2 days)
Office processes
account for up to 80% of the lead-time in the manufacturing and service
industries. The results of waste in the office - such as delayed response to
customer orders or incorrect billing - can be costly. Eliminating office waste can help
organizations achieve cost-effectiveness, customer satisfaction, and
profitability.
Office processes are
composed of a series of individual tasks. They are usually developed over many years and
contain steps that do not add value. In
some cases, official processes to get things done may not even exist, leading
to confusion and conflict.
A lean office is one
where each process has been streamlined for maximum value and efficiency. Error-proofing tools are used to minimize
opportunities for mistakes to occur. The
result is processes that work well for customers and employees alike, reducing
frustration while increasing quality and cost-effectiveness.
Lean Office is not
about cutting staff and resources. Instead, it is about optimizing employees’
efforts toward:
- Creating value for
the customer,
- Eliminating waste,
and,
- Speeding up the
operation by eliminating idle time created by paperwork and bureaucracy.
Workshop Outline
By the end of the workshop, you will be able to:
- Explain key
principles of Lean
- Differentiate
between a Lean Office and a regular office
- Create a basic value
stream map
- Calculate lean metrics that support Lean Office implementation and sustainability
- Describe the tools
of Lean Office and their applications, including:
- Apply a minimum of
seven Lean Office tools in response to a live office simulation
Learners will participate in a live office simulation. Through the use of discussion, presentations,
examples, and small-group work, learners will apply Lean Office principles and
tools to the simulated office to improve its operation. The workshop will be highly hands-on and
interactive. Learners will be provided
with a workbook containing information about each tool that will be a valuable
resource for back-home application.
|
|
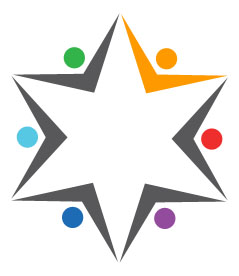 |
(2 days)
"It is good to catch and fix mistakes. It is even better to make it impossible to make mistakes!"
Poka Yoke is a quality practice focused on the prevention, early detection, and early remediation of mistakes in the production of goods or services. It relies on smart, simple, low-cost methods to make it easier for workers to do things right than to make mistakes! It saves organizations the huge costs of material waste, rework wages, and rework delays. It keeps processes flowing efficiently and smoothly.
The three principles of Poka-Yoke are:
- Design the process so that wrong actions are more difficult or impossible to make.
- Design the process so that mistakes become immediately obvious to the employee so that s/he can correct it immediately.
- Have the process detect errors as early as possible so that downstream consequences are prevented.
Examples of Poke Yokes include:
- Electronic forms that will not accept data outside of a specific range of values;
- Color-coded paperwork that helps ensure each party receives the correct version;
- Standardized containers a a workstation enables the employee to know exact quantities of an item without having to weigh or count the contents;
- A drill can be rigged to stop immediately when the bit contacts grounded or electrically live materials so it can't drill through hidden pipes or wiring.
Workshop Outline
Participants will assess the need for Poka Yokes, design them, and apply them to office and manufacturing processes.
Key topics include:
- The cost of making mistakes
- Human-error-causing conditions
- Principles of Poka Yoke
- Examples of manufacturing Poka Yokes
- Examples of office Poka Yokes
- Examples of service Poka Yokes
- Categories and types of Poka Yokes (applicable across industries)
- Process mapping basics
- Assessing and quantifying process risk
- Identifying where in the process to insert Poka Yokes
- Determining the type of Poka Yoke that will work best in the situation
- Step-by-Step Process for Implementing Poka Yoke
- Integrative practice and feedback; small teams will each work on appropriate case studies from the manufacturing, office, or service sector.
The workshop will be highly interactive, and will include a significant amount of hands-on practice.
|
|
|
(3 days)
Option: if your organization provides confidential access to company process data and invests in my time for the initial data “clean up” and analysis , this
workshop can be completely built around your KPI, a current transactional or
manufacturing process, and the insights that can be found through graphical data
analysis. Otherwise, generic data will
be provided and used.
In order for any organization to achieve its business goals and
reach the standards represented by its Key Performance Indicators (KPI), many
steps of many processes must work effectively.
As a leader (executive, director, manager, supervisor, or quality specialist) you are responsible for ensuring processes work
efficiently and effectively; you are also responsible for improving
them. With the complexity of the
business and so many factors to consider, it can be difficult to determine
where to invest time, energy, and other resources in order to receive the
greatest return.
In this workshop, you will learn to apply basic descriptive
statistics and graphical analysis tools to your organization's data.
You will be able to identify the relationship
between a KPI result and important factors related to its production. By appropriately graphing relationships
between process inputs, process outputs and KPIs, you will be better able to
identify which factors to change in order to improve KPI results.
It is important to note that graphical analysis, while extremely useful and simple to use, is not as
accurate as full statistical analysis. However, the concepts and tools learned
during this workshop will lay a solid foundation for learning to perform
statistical analysis in the future. In
the meantime, graphical analysis will provide you with tools you can use to understand, describe, analyze, and communicate process information, identify high-value
targets for improvement efforts, and measure and communicate the results to
other managers and business leaders.
Workshop Outline
The workshop will include discussion and practice of the
following:
1. The Relationship between Processes, Data, and Business
Results
- Y = F(X), or, Process Outputs vs. Process Inputs
- Process Specifications: Target, Upper Spec Limit, Lower Spec
Limit
- Benefits of Measuring both Inputs And Outputs
- Variation and the Problems It Causes
- Common Cause vs. Special Cause Variation
- Relationship to the Process Map
- Relationship to the Fishbone Diagram
- Relationship to the Plant KPIs
2. Basic Statistics
- Mean, Median, and Mode
- Standard Deviation
3. Three Types of Data
- Continuous
- Defectives
- Defects
- Different Analytical Tools for Each Type of Data
4. Representing and Analyzing Data Using Charts
- Selection Grid for Choosing an Appropriate Chart
- Pie Charts
- Histograms
- Pareto Charts
- Run Charts
- Box Plots and Multiple Box Plots
- Dot Plots and Multiple Dot Plots
- Normal Probability Plot
- Scatter Plot and Matrix Diagrams – finding correlations
- Multi-Vari Charts – finding out what makes a difference or
not
- Control Charts – identifying the presence of Special Cause
Variation
- Practice Making Charts
5. Skills Practice and Integration
- Participants will apply their skills through a case study
that includes:
- A process that produces a product or service
- Product/service specification limits
- A KPI-related issue
- A process map
- Fishbone diagram
- Process-related data for both Y and X's
(If the customized option is chosen, the skills practice will be
based on a current process used by your organization and actual data from the process)
In the case study, participants will be asked to:
- Define the KPI-related issue to be explored using graphical
analysis
- Review the process map
- Calculate basic statistics
- Identify the types of data being used
- Check the data for normality and Special Cause Variation
- Graphically analyze the data using the full range of charts
- Relate the results of the analysis back to the initial
process and KPI issue
- Determine potential high-value solutions and next steps
|
|
|
(3 days; Prerequisite of "Using Graphical Data Analysis to Improve KPI and Processes" workshop, or equivalent)
Business processes may be tracked to produce numerical data. However, data by itself is meaningless.
Statistical analysis can be used to analyze numerical data to provide surprising and useful insights about what really works - and does not work - in a process. This information can be used to convince key decision-makers about the size and nature of the problems faced. Resources can be focused on solving the right problems using the right approaches. When applied in this way, statistical analysis can greatly reduce the time, cost, and risk required to effectively solve problems.
In this workshop, participants will learn to select appropriate statistical analysis tools, apply them using statistical analysis software, and interpret the results in terms of understanding and solving a business process problem.
Workshop Outline
By the end of the workshop, you will be able to:
- Recap key concepts from the "Using Graphical Data Analysis to Improve KPI and Processes" workshop, above
- Explain the purpose and meaning of the following statistical tools, and apply and interpret them to solve practical problems:
- Process Capability and Process Performance, or Sigma level (Zp(d), First Time Yield, Defects per Unit, Zlt, Zst, Zshift, Zbench, Cp, Cpk)
- Hypothesis Testing
- Distribution Identification
- Confidence Intervals
- 1-sample T-Test
- 2-sample T-Test
- 2-Proportion Test
- 2-Sample Standard Deviation Test
- ANOVA
- 1-Sample Wilcoxon Test
- Chi Square Test
- Kruskal-Wallis Test
- Mann-Whitney Test
- Regression Analysis
The workshop will provide just enough theory that the tools can be understood, applied, and interpreted. The main focus will be on using the tools to understand and resolve business problems. There will be significant hands-on practice based on practical workplace problems.
Participants will require access to a laptop during the workshop.
The client may choose from several different widely-available software packages, with a variety of features and price points.
|
|
|
(1 day)
In most organizations, there is a wide variety of improvement projects for
managers to choose from. It is important to choose projects that will deliver the greatest value to the organization. However, senior
management are not as familiar with the details of the operation and how each potential project affects the bottom line. Key
questions asked by senior management about each project will likely include:
- How much money will it save?
- What are you changing?
- How does changing that lead to savings?
- What costs and revenues did you include in your
estimate? Why?
- What method did you use to make your estimate?
- Could implementing this project have any negative impact on safety, quality, customer relations, workers, or reputation?
In this workshop, you will learn how to build project-specific models for calculating the project's financial and non-financial
benefits. Emphasis will be
placed on the need to use existing data to determine logical, truthful, justifiable, project-specific responses to senior management questions.
Workshop Outline
1. Introduction
- What is a Project Benefit?
- What is a Benefit Model?
- The Balanced Scorecard Approach
- Cost-Benefit Analysis
2. Different Perspectives on the Value of Benefits
- Business-Level Benefits
- KPI Benefits
- Operational Activity or Process Benefits
- Benefits are in the Eye of the Beholder
3. Types of Project Benefits
- Hard vs. Soft
- Quantifiable vs. Nonquantifiable
- Approaches to Quantifying the Unquantifiable
4. Cost-Model Methods
- Types of Project Costs
- Traditional Costing
- Activity-Based Costing
5. Methods of Estimating
- How’d You Get that Number?
- WAG and SWAG
- Past Performance
- Pilots or Trials
- Analogies
- Executive Auction
- Benchmarking
6. Timing Counts
- When to Make an Initial Prediction
- When to Revise
- The Problem at Project End
- The Post Implementation Review
7. Guidelines for Success
- Summary of Best Practices
- Group discussion of application within your organization
|
|
|
(5 days)
This workshop is designed to provide learners with the foundational
tools needed to
- Identify and prioritize potential process improvement projects
- Define projects
- Create and implement a data collection plan that will provide useful information about the problem
- Graphically analyze data collected to identify root causes
- Identify, prioritize, and design needed process improvements, and
- Develop and implement a control plan that includes error
proofing and statistical process control.
The workshop is based in Lean Six Sigma principles and
methodology. In essence, it consists of
half of the traditional Green Belt course.
Workshop Outline
1. Introduction
- Principles of Process Management
- Lean Six Sigma
- Lean Six Sigma Project Stages
- Project Roles
2. Define Phase
- Project Selection
- The Business Case
- Voice of the Customer
- Customer Dashboards
- Drilldown
- Quality Function Deployment
- SIPOC/COPIS
- ARMI
- Pareto Chart
- Business Process Map
- Frustration Lens
- Cause and Effect Diagram
- Group Voting
- Includes/Excludes
- Vision: More of, Less of, Stay the Same
- Project Scope Contract
- Responsibility Grid
- We Know/We Need to Know
3. Measure Phase
- Process Units
- Targets, Spec Limits, and Defects
- Variation
- Populations and Samples
- Steps in a Data Collection Plan
- Sampling
- Data Types
- Y = f(x)
- Graphical Representation of Data
- Descriptive Statistics
- The Normal Distribution
- Calculating Process Performance: Z-Long-Term or Z-Bench
- Checking Continuous Data for Normality and Stability
- Process Performance vs. Process Capability
- Control vs. Technology Chart
- Calculating Zst Using Different Types of Data
- Summary Chart: Data Type and Process Performance
- Z Table or P(d) Table
- Probability Distributions and Mathematical Models
4. Analyze Phase
5. Improve Phase
- Lean Lab: Key Lean Concepts, Tools and Calculations
- Value-Added vs. Waste
- Best Practices in Process Design
- SCAMPER
- Payoff Matrix
- Pilot the Intended Changes
6. Control Phase
- Control Plans
- Monitoring Signals
- Process Stability
- Failure Mode and Effects Analysis (FMEA)
- Error Proofing
- Inspection
- Procedure and Process Documentation
- Checklists
7. Integration - Application of Key Learnings
|
|
|
(9 days plus reading and practical assignments; may be divided into several workshops if preferred)
A Lean Six-Sigma Black Belt is someone well-qualified to lead business process improvement projects within their department as part of their job. A Greenbelt can apply statistical analysis and group process techniques to business problems to resolve them. Greenbelts typically save their employers many multiples of their salary annually, while still performing their regular work as managers, or part of their regular work as front-line employees. The depth of technical knowledge, leadership skills, and the improvement mindset developed while leading improvement projects makes experienced Greenbelts prime candidates for internal promotion, ensuring a qualified pool of succession candidates. Customers and employees appreciate that processes work faster and produce higher quality products or services. Leaders appreciate the cost savings and loyalty that result.
This 10-day program will prepare participants to identify, classify, lead, and apply Lean Six-Sigma tools to business improvement projects. Upon completion of the program, participants will be prepared to write their organization's internal Greenbelt exam or a reputable publicly-available exam, such as that offered by the American Society for Quality (ASQ).
We currently offer this program in partnership with Dalhousie University. This link will take you Dalhousie's website where you can see a detailed course description and schedule of public course offerings. Please note: the Dalhousie program includes a certification exam at no additional charge!
Workshop Outline
The program will provide the concepts, tools, written material, practice and feedback needed to successfully write a Lean Six-Sigma Greenbelt exam.
Specific topics include ALL of those listed in ALL of the workshops, above. In addition, the following topics will be addressed:
- Measurement System Analysis
- Design of Experiments
- Statistical Process Control Charts
- Project Team Leadership
- Managing Stakeholder Relationships
- Effective Sponsor Relationships
- Project Planning
- Project Hand-off and Closure
The workshop will be organized and delivered according to the five phases of a Six Sigma project:
- Define
- Measure
- Analyze
- Improve
- Control
The workshop will be very interactive, and will include many practice and feedback opportunities. Participants should be prepared to read articles and complete practice assignments outside of class hours as needed.
|
| |